Scuba Tanks
Scuba cylinders are probably the most recognizable piece of scuba equipment. They are capable of storing a large amount of compressed air, and this allows divers to remain underwater for extended periods of time. However, the high pressure of this compressed air presents possible hazards to divers, so a thorough understanding of this important piece of equipment is essential for your safety.
On this page, you'll learn about the different types of cylinders available, the valves that open and close the cylinder, and required maintenance procedures.

Cylinder Materials
Scuba cylinders are filled to air pressures ranging from 2000 to 3500 psi (pounds per square inch). To withstand this high pressure, cylinders are carefully engineered from two common materials: steel or aluminum. Both materials have benefits and disadvantages.
Steel Cylinders
Steel is stronger than aluminum, which allows the walls of steel cylinders to be thinner than aluminum tanks. This results in a smaller physical size than aluminum cylinders of the same capacity. The increased strength also makes steel cylinders more resistant to exterior damage. Unfortunately, steel rusts, so special care must be taken to avoid allowing water to enter the cylinder.
Aluminum Cylinders
Aluminum cylinders are popular because of their lower cost. Another advantage is that aluminum doesn't rust. But these cylinders also have some disadvantages. Aluminum is softer than steel, so they can be dented when dropped or knocked over. Also, the cylinder walls must be thicker to compensate for aluminum's weaker strength. This results in a larger physical size than steel cylinders of the same capacity. Aluminum is also more buoyant than steel, so you'll need to wear more weight when using aluminum cylinders.


Capacity and Pressure
A cylinder's capacity indicates the volume of uncompressed air a cylinder holds when filled to its maximum rated pressure. For example, if you have an 80 cubic foot cylinder, 80 cubic feet of uncompressed air can be compressed into that cylinder. The capacity of most cylinders ranges from 50 cubic feet to 120 cubic feet.
A cylinder's maximum service pressure refers to the maximum pressure a cylinder can be filled to, and this determines the physical size required to contain the rated capacity of air.
The illustration to the left demonstrates the relationship of capacity and pressure. As you can see, increasing capacity without increasing the maximum service pressure results in a larger cylinder, while increasing the maximum service pressure allows a cylinder with a smaller physical size to hold the same amount of air.

Cylinder Markings
All cylinders have important specifications stamped around the top of the tank. The location and format may vary between manufacturer, but with practice you'll learn to recognize key specifications and what they mean.
- DOT Stamp
- Many countries, including the United States, require a cylinder to be approved by a government agency. Cylinders used in the United States must be approved by the Department of Transportation (DOT). Cylinders manufactured before 1970 will have the letters "ICC" instead of "DOT."
- Cylinder Material
- As you have already learned, cylinders can be made out of either steel or aluminum. Steel cylinders are stamped with the characters "3AA." Aluminum cylinders, like the one illustrated to the left, are stamped with the characters "3AL."
- Maximum Pressure
- All cylinders are stamped with their maximum filling pressure. The location varies by manufacturer, but becomes easier to identify when you become familiar with common maximum service pressures. Common pressure ratings include 2250, 2500, 3000, and 3500 psi.
- Serial Number
- All cylinders are stamped with a unique serial number for identification purposes. The format of the serial number varies by manufacturer.
- Manufacturer
- All cylinders are stamped with an identification of the manufacturer.
- Hydro Test Date Stamp
- All cylinders must pass a hydrostatic test every five years. The test date is permanently stamped on the cylinder if it passes inspection. In this example, the test was performed in June of 2001. A plus "+" symbol following the test date indicates the cylinder can be filled 10% higher than the stated maximum service pressure. Because this test is performed every five years, the cylinder may have several hydro dates stamped on the cylinder.
- Capacity
- Most aluminum cylinders have their capacity stamped on the cylinder. This is not a required specification, and very few steel tanks have a capacity stamp.

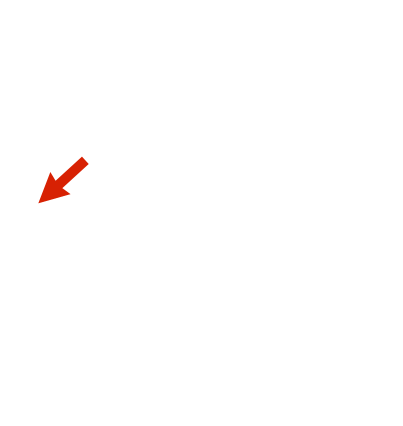
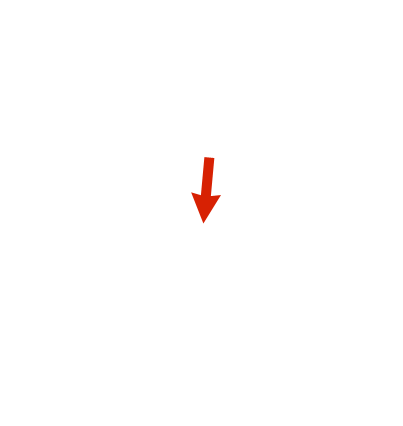

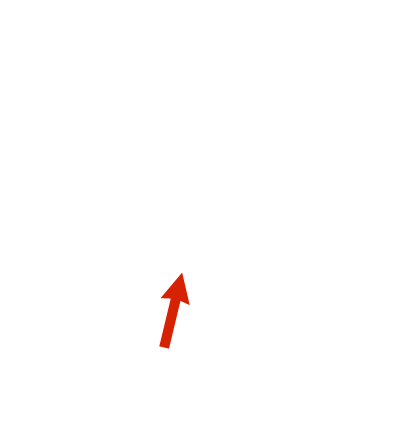

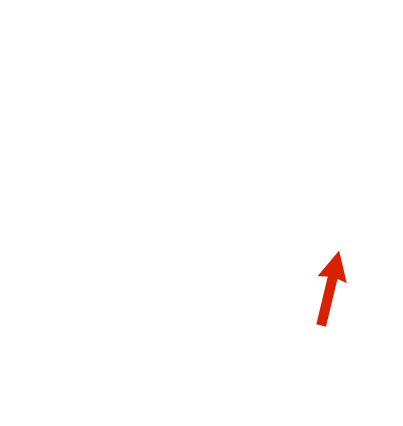
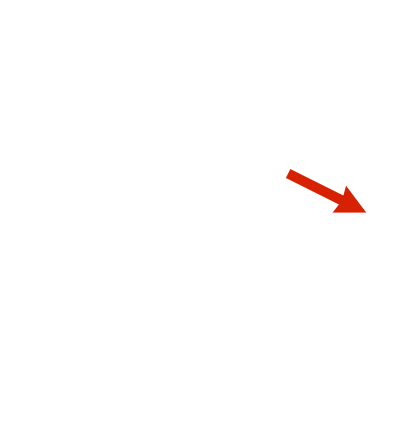
Valves
A cylinder's valve opens and closes the tank. There are several styles available, but all have some common components.
- Valve Knob
- The knob opens and closes the valve. Turning the valve clockwise closes the valve, and a counterclockwise turn opens the valve.
- Valve O-Ring
- The o-ring creates the seal between the valve and regulator (covered in the next lesson).
- Burst Disk
- A burst disk is a thin copper disk that's designed to rupture if the cylinder's internal pressure reaches a certain level. This important safety feature helps prevent the cylinder from rupturing, which could result in serious bodily injury.
- Valve Snorkel
- The valve snorkel is a tube that extends from the bottom of the valve. This prevents debris from flowing through the valve when the cylinder is inverted.

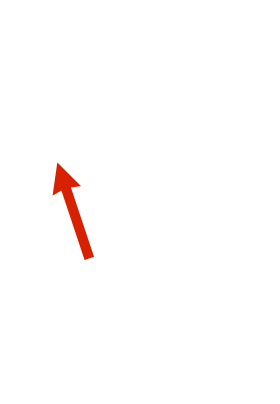



"K" Valve
Valves are available in several styles, but as a beginning scuba diver, you only need to be familiar with the three common styles. These are the "K" valve, "J" valve, and DIN valve.
"K" valves are the simplest of all valves, and are found on most modern cylinders. These valves fit regulators with yoke attachments. The regulator is attached by slipping the yoke attachment over the valve and tightening a screw against the rear of the valve.
The o-ring on a "K" valve is expanded by air pressure, and this expansion creates the seal between the regulator and valve. Over time, the o-ring may crack, wear out, or fall out, so it should be inspected before attaching the regulator.

"J" Valve
"J" valves are similar to "K" valves. What makes the "J" valve unique is a reserve mechanism. This is a spring-loaded valve that closes airflow when the cylinder's pressure drops below about 500 psi. The reserve is then opened by pulling a rod that's attached to the reserve lever.
"J" valves are no longer considered to be an acceptable method of monitoring your air supply because reliable cylinder pressure gauges have become standard equipment. For this reason, if you use a cylinder that's equipped with a "J" valve, it's important that you disable the reserve mechanism to prevent your air supply from being shut off while you still have air remaining. To disable the reserve mechanism, turn the reserve lever to the down position prior to your dive.
DIN Valve
DIN valves are installed on cylinders with service pressures exceeding 3000 psi. These valves are designed for use with regulators equipped with DIN attachments instead of yoke attachments. The regulator is attached by screwing its DIN fitting into the valve's internal threads.
With these valves the o-ring is attached to the regulator instead of the valve. The o-ring is thicker than yoke valve o-rings, and is more dependable. This system is sometimes referred to as a "captured o-ring."

Rinsing And Storing Scuba Tanks
Like all gear, tanks should be rinsed with fresh water after every diving day. This prevents corrosion from forming on the cylinder and valve. If the cylinder has a plastic or rubber tank boot on the bottom, remove it on occasion and clean the bottom.
Water is a tank's enemy, so you never want it to enter the inside. To prevent moisture from entering the tank, always store it with at least 200 psi of pressure.
Tanks are heavy and can cause damage if tipped over. So when storing or hauling your tanks, either lay them down or secure them so they cannot tip over.
Heat increases the tank's internal pressure, so store them away from sources of heat. An increase in temperature can cause the burst disk to rupture.

Filling Your Scuba Tanks
Tanks must be filled with clean, dry air. For this reason, always make sure you fill your tanks at a reputable scuba shop or resort. These sources maintain their compressors to ensure all oil and water is filtered from the air before it enters your cylinder.
If you smell or taste strange odors in your air, it may be contaminated with oil and should not be used. Immediately report the problem to the shop that filled the tank. Have your cylinder professionally cleaned or inspected before using it again.

Cylinder Inspections
Two tests must be periodically performed on all cylinders used in the United States. These are visual inspections and hydrostatic tests. When renting or purchasing a cylinder, you should check to make sure both of these tests are current.
Visual Inspections
Visual inspections must be performed on an annual basis. During this test the inside and outside of the cylinder is inspected for signs of cracks, pits, rust, or corrosion. The test date is marked on a sticker that is placed on the tank as evidence of the inspection.
Hydrostatic Test
A hydrostatic test must be performed every five years. During this test the cylinder is overfilled to a specified amount and its permanent expansion is measured. If the cylinder meets passing criteria the test date is permanently stamped on the cylinder.
